Чтобы вам не пришлось ремонтировать, будь то тапочки или атомный крейсер, надо для начала определить какие параметры ремонтируемого объекта вышли за нормы, установить возможность восстановления данных параметров и составить план ремонта. Головка блока цилиндров в этом плане ничем принципиально не отличается. Без правильной дефектовки и определения правильной последовательности выполнения работ по ремонту ГБЦ, говорить о качественном и экономически разумном ремонте просто смешно.
Сразу хочу сказать , такие этапы как: разборка головки, демонтаж клапанов, очистка головки и клапанов в этой статье рассматривать не буду. Эти работы могут показаться простыми и не ответственными, это не так. Без чистоты агрегатов взятых в ремонт, нельзя говорить о каком либо качестве последующих работ. Также на этапе разборки головки и демонтажа клапанов, некоторые люди умудряются столько дров наломать, что иногда дальше можно не ремонтировать. Однако я эти вопросы оставлю пока в покое, им надо будет посвятить отдельную статью. Так же не рассматриваю здесь вопросы тестирования головки на герметичность (опрессовки). Будем дефектовать головки, которые прошли разборку, мойку, опрессовку и приняты к дальнейшему ремонту.
Итак, что будем рассматривать:
— необходимость обработки плоскости ГБЦ;
— состояние направляющей втулки клапана и необходимость её замены;
— состояние клапана и возможность его восстановления;
— состояние рабочих фасок седла клапана и возможность их обработки;
— состояние сальников клапанов и необходимость их замены;
Привалочная плоскость головки блока цилиндров.
Для диагностики привалочной плоскости головки блока цилиндров необходимы следующие инструменты: лекальная линейка необходимой длинны, набор щупов, штангенциркуль или рейсмус высотомер с точностью до 0,05 мм и технические данные по проверяемой головке с допустимой величиной зазора и допустимой остаточной высотой.
До измерения прогиба головки, на помытой и очищенной от нагара и остатков прокладки головки, выявляем видимые на глаз проблемы. Такими могут являться механические повреждения, коррозия материала головки, раковины возникшие в местах прогара прокладки ГБЦ. Определяем возможность обработки по внешним видимым признакам, возможно головка требует наплавки поврежденных мест либо других восстановительных мероприятий. Особое внимание уделяется местам уплотнения прокладки вокруг цилиндра, уплотнения водяной рубашки и масляных каналов. Если при таком осмотре дефектов определяющих объем работ не установлено, переходим к проверке плоскости головки на прогиб инструментальным способом.
Проверка проводится на агрегате имеющем комнатную температуру (если проводилась опрессовка, головка должна остыть!). Прикладываем линейку сначала в двух — трех местах по длине головки, а затем по двум диагоналям пытаясь засунуть под нее щуп. Начинать надо с самого тонкого щупа, обычно это 0,05 мм. Если он не проходит под линейку ни в каких местах, необходимости шлифовки плоскости нет. Чем чаще ваши попытки вставить щуп под линейку, тем выше вероятность найти вогнутое место. Величину допустимого прогиба надо искать в ремонтных пособиях или рекомендациях производителей. С учетом собственного опыта могу сказать, что прогиб 0,01мм на 100мм длины допускают практически все автомобильные производители.
Еще один важный момент, если обработка плоскости производится методом мокрой шлифовки, то можно такую работу рекомендовать без проверки головки на плоскость. Этот метод позволяет снять с головки ровно столько, сколько необходимо. Если обработка производится методом резания (фрезеровка), такую обработку без необходимости лучше не делать, так как при таком способе снимается гораздо больший слой материала и сокращается количество последующих шлифовок.
Кроме того существует еще один немаловажный фактор, остаточная высота ГБЦ. Проводим измерения высоты головки с помощью штангенциркуля или рейсмуса и сравниваем с техническими данными. Здесь можно отталкиваться только от рекомендаций производителя и пожеланий моториста. Часто «умные» заказчики вычитывают в рекомендациях производителей, что обработка плоскости головки данной модели не допускается. Рекомендую задуматься таким умникам, как она будет ездить кривая.
В любом случае окончательное решение по всем обработкам деталей двигателей за заказчиком.
Направляющая втулка клапана.
Для диагностики направляющих втулок нам необходимы следующие инструменты: нутромер с диапазоном 5 – 12 мм, индикаторная стойка, индикатор часового типа с точностью шкалы 0,01 мм.
Диагностика направляющей втулки клапана, вещь вроде бы обыкновенная, однако вы мало найдете людей, которые вам толково смогут объяснить, почему необходимо менять втулку. Обычно это происходит так: слесарь вставляет клапан в направляющую втулку, начинает шатать клапан, и выдает: «Смотри! – Болтается!». А как же в этом случае тепловой зазор между клапаном и втулкой? Клапан не может не болтаться, иначе он заклинит! Мерительные инструменты для таких измерений не очень удобны, во первых, измерять много мелких отверстий нутромером это долго, а во вторых учитывая неравномерный износ втулки, точность таких измерений не высокая.
Начинаем как обычно с внешнего осмотра, смотрим на ножку клапана: если на ней существуют задиры, потянутости – направляющую втулку клапана надо однозначно менять. Если на рабочей части ножки клапана нагар, надо смотреть какой и сколько. Он обычно возникает на клапане со стороны цилиндра, особенно на выпускных клапанах. Величина нагара до 20 мм по рабочей части ножки клапана ни о чем не говорит, 20-30 мм надо мерять втулку, более 30 мм направляющая втулка изношена и газы забивают в повышенный зазор между клапаном и направляющей. Если по внешним признакам принять решение о замене направляющей не удалось, переходим к измерениям. Как я уже говорил, можно измерять износ втулки с помощью нутромера, но мы с вами рассмотрим другой способ измерений более удобный для применения на практике. Мы будем измерять люфт клапана в направляющей втулке с помощью индикатора, и вычислять зазор между клапаном и втулкой.
Для того чтобы померять люфт клапана на ровной поверхности укладываем головку привалочной плоскостью вверх и вставляем клапан в направляющую (желательно чтобы верхние концы направляющих упирались в ровную поверхность). Верхний край направляющей должен быть на одном уровне с верхним краем клапана, как показано на рис. 1. Устанавливаем индикаторную стойку на головку таким образом, чтобы наконечник индикатора упирался в торец головки клапана и пошатывая клапан (без излишних усилий) меряем величину люфта. Дальше чтобы вычислить величину зазора прийдется вспомнить школьный курс геометрии, можно тригонометрию или проще теорему, о подобии треугольников. Исходя из теоремы о подобии треугольников и глядя на рис.1 , получим следующее:
Зазор=(Люфт*Длина направляющей)/(2*Длина клапана)
То есть, величина зазора равна величине люфта клапана, умноженной на длину направляющей и деленной на две длинны клапана. Дальше осталось полученный зазор сравнить с ремонтными допусками и принять решение о необходимости замены направляющей.
В дальнейшем можно наоборот вычислить допустимый для этой модели люфт кпанапа:
Люфт=(Зазор*2*Длину клапана)/(Длину направляющей)
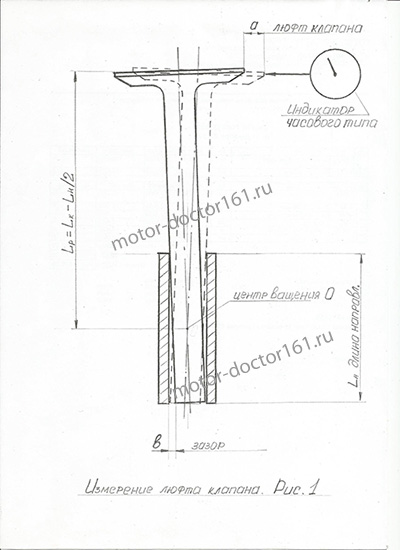
Если направляющие втулки имеют газовый карман, следует учитывать только фактически работающую длину втулки. Также при отработке подобных измерений, на начальных этапах следует контролировать расчетные величины с помощью нутромера.
Клапан.
Для диагностики клапанов нам необходим микрометр с диапазоном 0-25 мм, устройство для проверки клапана на биение с индикатором или станок для шлифовки клапанов.
И так как обычно внешний осмотр, смотрим на ножку клапана: если на ней существуют задиры, потянутости, заметная на глаз, или на ощупь выработка – клапан подлежит замене. Также подлежат замене клапана с большой выработкой либо глубокими раковинами тарелки. Далее клапана с ровными гладкими ножками необходимо проверить на биение. Для этого существуют различные приспособления, одно из них изображено на фото ниже. Клапан прижимается к неподвижной станине, его торец ставиться в упор, лапка индикатора прижимается к тарелке клапана. Далее вращая клапан, смотрим биение шляпки относительно оси вращения, если оно более 0.05 мм — клапан бракуем, меньше — подлежит шлифовке.
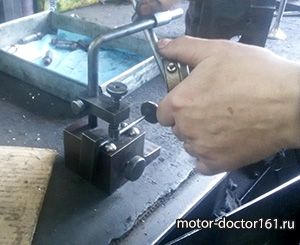
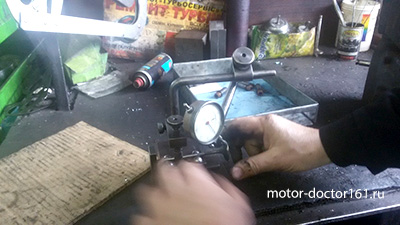
Другой вариант проверки клапана на биение – установить его на шлифовальный станок, и сделать касание шлифовальным камнем. Если клапан достаточно ровный, вы услышите звук равномерной обработки. Если вы услышите чиркание клапана об камень – клапан непригоден.

Седло клапана.
Для диагностики состояния седла клапана понадобиться измерительная планка с индикатором часового типа или микрометрисеский глубиномер, на мой взгляд планка с индикатором гораздо удобнее. Для грубой проверки подойдет даже штангенциркуль с глубиномером.
Диагностика седла клапана сводится в большинстве случаев к выбору: менять седло или обработать фаску существующего седла. Случай: « с седлом делать ничего не надо» не рассматриваю, если принесли головку на дефектовку – значит что то делать необходимо. Навряд ли вам принесут новую головку в ремонт, или головку снятую с нового двигателя.
Итак – дефектовка седла! Определяем по внешним признакам общую пригодность седла клапана. Трещины, неровности на седле, глубокие раковины, следы ударов от попадания посторонних предметов а также черезмерно изношенная рабочая фаска седла клапана говорит о необходимости замены седла.
Если по внешним признакам, выявить дефекты седла указывающие на необходимость замены не удалось, переходим к инструментальной дефектовке. Важнейшим показателем износа седла клапана являеться положение клапана в головке относительно привалочной плоскости, или в некоторых моделях (чаще бензиновых двигателей) вылет торца клапана относительно оси распредвала. С помощью планки с индикатором, измеряем утопание клапана относительно плоскости (в некоторых моделях клапан выступает над плоскостью) и сравниваем этот показатель с допустимым значением. Если губина залегания клапана больше допустимой величины – седло клапана необходимо заменить. В случае когда залегание клапана менее чем на 0,2 мм приближено к минимально допустимому показателю, я бы рекомендовал также замену седла. Это связано с последующей обработкой фаски, при которой клапан сядет еще немного глубже. После измерения утопания седла (а на бензиновых двигателях вместо него) , необходимо проверить вылет штока клапана. Особенно важно проверять вылет штока клапана на двигателях с гидрокомпенсаторами и двигателях, где регулировка зазора в клапанном механизме производится с помощью шайб. Для таких моделей большое значение имеет остаточная высота головки, которую также необходимо учитывать при проведении диагностики седла.
Сальники клапанов.
Сальник клапана надо менять при любой ревизии головки блока цилиндров! И всеже укажу признаки износа сальников клапанов при которых их нельзя оставить даже в самом крайнем случае. Разрывы сальников, затвердевание резиновой обоймы сальника, сползание сальника с направляющей втулки клапана и перекосы сальника на посадочном месте. Также в случае замены направляющей втулки клапана однозначно устанавливается новый сальник клапана.
В следующей статье рассмотрим с вами правильную последовательность работ при ремонте головки блока цилиндров.